This job was a bit of a challenge right from the start. By the time I was called in, the stairwell had already been formed, and the walls were up.
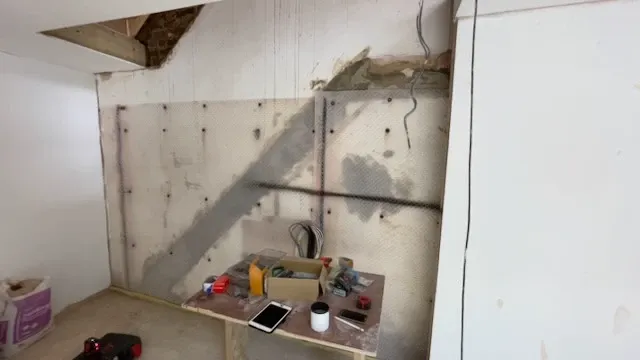
Normally, this isn’t too big of an issue, but on this particular project, the space left for the staircase posed a problem. The customer wanted a 3-winder staircase with deeper treads, but the bulkhead in the stairwell meant I couldn’t achieve the 2 metres of headroom required to meet building regulations.
To make things trickier, this staircase was leading into a basement, and the walls had been tanked to protect against damp. Fixing the staircase directly to the tanking wasn’t an option, as it would compromise the waterproofing.
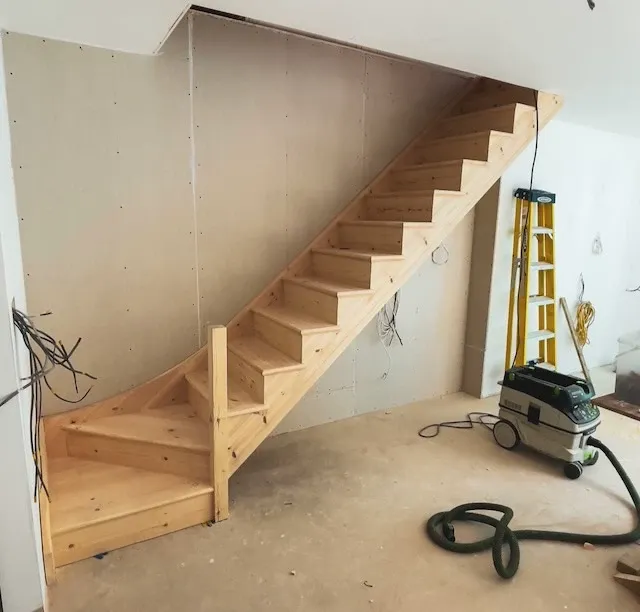
After assessing the situation, I came up with a solution. I reduced the tread depth to the minimum allowed and adjusted the design to a 2-winder staircase instead. This gave me just enough headroom to meet regulations. To address the tanking issue, I built a stud wall in front of it, allowing me to securely fix the staircase without interfering with the waterproofing.
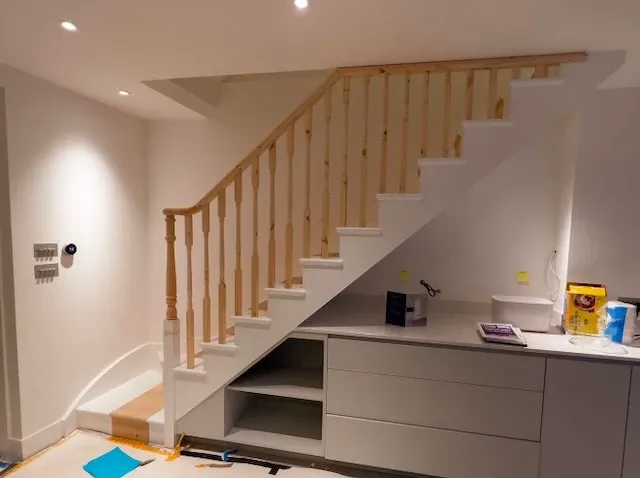
A couple of weeks later, after the plastering was finished and decorating had begun, I returned to fit the balustrading. We matched the handrail and spindles to the balustrading in the rest of the house for a seamless look.
In the end, the customers were really pleased with the result, and it was rewarding to see everything come together despite the initial hurdles.